Scientific Report 979
This report is also available as a PDF document .
Abstract
As part of the NERC Macronutrient Cycles Programme (MCP), a small pump-priming grant was awarded to the University of York for the construction of a prototype ‘SkyGas’ system. The concept behind this Technology Development grant was to construct a prototype ‘fly-bywire’ automated system for monitoring terrestrial greenhouse gas (GHG) fluxes; a ‘world first’ that, if successful, could contribute significantly to the NERC strategy on climate change research. The concept was to build a field system (30 m x 30 m) for automated monitoring of GHG fluxes from land and water surfaces, developing entirely new technologies. Close collaboration between the Electronics and Biology Departments at York have resulted in such a prototype SkyGas system being successfully constructed on York campus and, after initial commissioning of the equipment, the electronic engineers suggested that both the accuracy and operation of the system may be greatly enhanced by incorporating capability for locating the moving ‘chamber head’ in real time using, for example, advanced differential GPS capability. For this reason a request for a GEF loan of two GX1230 Differential GPSs was made to test the extent to which incorporation of GPS technology could improve the building and `flight’ control for this new SkyGas technology. After discussion with the GEF team we requested, and were subsequently loaned, two GPS systems together with training in their use. During the loan it became clear that performance of the prototype SkyGas system would not benefit significantly from the incorporation of high resolution GPS, but it was obvious that GPS (or laser control) could be extremely useful when moving on from this prototype to planned larger, full size (football pitch scale) installations. The equipment loan was essential in showing the potential for incorporation of GPS technology into future up-scaled SkyGas systems.
Background
The on-going NERC-funded MCP is charged with quantifying the major macronutrient cycles, and investigating their response to a changing C cycle. This research initiative is committed to quantification of bi-directional transfers of C and N between atmosphere-terrestrial and atmosphere-aquatic systems, and requires measurements of key gaseous fluxes (particularly CO2, CH4, N2O, NH3 and NOx) at high spatial and temporal frequency. Key international and international decisions are currently being made about energy production, transport and, of particular relevance to the current NERC Macronutrient Cycles Programme (MCP), land use and catchment management yet, frequently, without a full quantification of GHG implications. In particular, data on the transfers of CO2, CH4 and N2O are at the forefront of these GHG data needs, where data acquisition is currently hindered by important technological gaps. There is frequently enormous variation in diversity of topography, vegetation type, underlying hydrology, etc. even over areas of just a few m2 and, added to this spatial complexity, is daily and seasonal variability, making the task of attempting to produce meaningful integrated gas flux data for terrestrial and freshwater systems very difficult. A major reason for the paucity of accurate flux data is the difficulty of making frequent measurements in complex and heterogeneous environments. We increasingly need measurements at smaller `field’ scales, enabling flux comparisons across heterogeneous landscapes or gradients (e.g. pastures, wetlands) and across field manipulations (e.g. fertilizer additions, crop trials) with an urgent need for new measurement approaches. Existing automated flux chambers frequently present problems of power supply, centralised gas analysis, expensive multiplexing, and cannot be easily applied to tall vegetation. Also, establishment of automated chambers in large numbers across spatially separated plots is prohibitively expensive. The overall aim of the current NERC-funded project was to develop a new type of automated GHG flux equipment.
In order to acquire high-frequency trace gas measurements at the field scale, we have designed a novel automated trace gas measurement system which is a flexible and cost-effective alternative to current manual or automated chambers. This new automated system `flies’ a chamber to any X-Y-Z co-ordinate within the field site by transporting it through the air using cables and winches between four towers in the corners of the site (see Fig. 1).
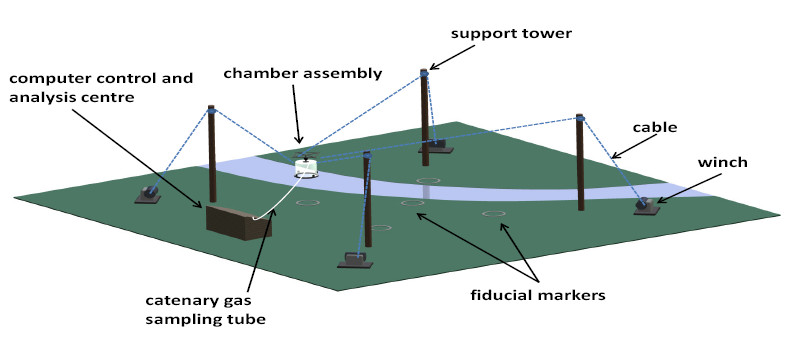
The basic 3D flying system mirrors the more expensive technologies used in camera and stage work, but we deploy a gas flux chamber in the head configuration. The system operates automatically under computer control, enabling different measuring cycles to be pre-programmed including specific sampling points, pathways or protocols across the field site. All mechanical and software development associated with SkyGas has been carried out by University of York staff and has involved a number of key areas for development, including electronic flight control, mechanical engineering, atmospheric gas analysis, chamber design, high frequency data analysis, etc.
Site location
The recently constructed Heslington East campus at the University of York includes specific wildlife ‘reserve’ areas containing natural vegetation and a complex of freshwater pools and rivers, and an area has been made available for use by the Biology, Physics and Chemistry Departments for construction of an Open-Air Atmospheric Chemistry Facility (53°56’41.59”N; 1°01’40.28”W). The site is only a few minutes walk away from the Departments of Biology and Chemistry, providing ease of access and security (Fig. 2); it was solely within this defined area where the loaned GEF equipment was deployed.
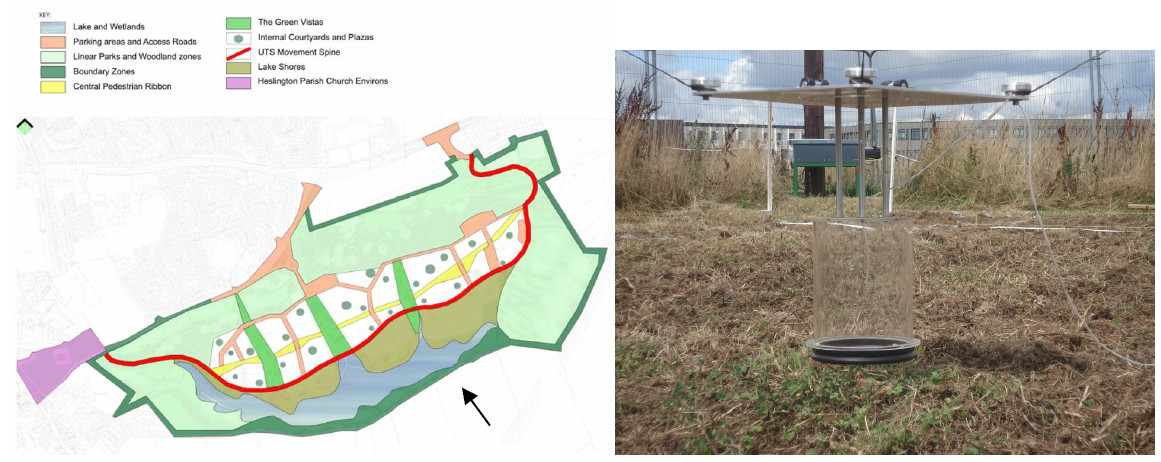
Role of GPS
One core requirement for the SkyGas system was a control system which required knowledge of the real-time location of the head in 3-D, to cm (X, Y, Z) accuracy, within the SkyGas arena. These data need to be relayed to the control centre (CC) and the four winches then individually instructed to move the head, under automatic control, through a specific series of X-Y-Z co-ordinates. This kind of problem is routinely encountered in aeronautical control systems and the necessary open loop algorithms are well proven and an area of expertise for which the Electronics Department at York is internationally recognised. Initial project design discussions led to the adoption of a simple index system on the winch feeds to inform the CC of the position of each winch rope in real time; this was considered a secure and inexpensive approach, although it was recognised that later developments could, ideally, utilise high specification GPS. Given current equipment limits within NERC grants, it was not possible to develop the more expensive GPS solution within the existing proof of concept grant, but the NERC GEF was an ideal opportunity to investigate the potential of GPS for the control aspects of the project. We predicted that incorporating differential GPS feedback would improve precision, flexibility of control and the ability to increase scale without loss of accuracy.
Survey procedure and data quality (including any recommendations for future borrowers)
We deployed the differential GPS system i) to accurately locate ‘landing points’ in the X,Y and Z planes within the arena, ii) by attaching to the moving chamber to investigate the feasibility of real-time dynamic location control and iii) attached to the moving chamber to test the precision and accuracy of repeated landings.
In order to achieve this we established a ‘base station’ on the CC roof and used the second GPS system in ‘roving’ mode. The GPS data were compared with fixed point ‘calibrated plates’ in fixed positions on the ground with pre-marked 2D mm grids. These comparisons showed that consecutive landings resulted in a cluster of GPS points for each landing area, with the majority of landing points being within ca. 9 mm of each other for the GPS and 3 mm for the fixed calibration plates. The GPS was indicating an accuracy of between 9 mm and 15 mm in terms of landing accuracy of the chamber but the points were in fact closer to each other, as indicated by the calibrated landing plates. Similar errors were found when using the GPS to locate fixed positions using repeated measurements. We found the equipment to be easy to use after appropriate training, was sufficiently robust for extensive field use and had the capability of providing real-time feedback positional data to the CC under all weather conditions.
Findings and Interpretation to date
It appears that, for a 30 m x 30 m SkyGas arena, the use of differential GPS as part of the control system offers no advantages over simple indexing of the winches and is ‘over-kill’. However, we have no measurements of comparative GPS and winch accuracy over a much large arena (e.g. football field scale) and suspect that an independent and absolute indexing system, such as that provided by differential GPS (or laser tracking), would be an important technical development at the next stage of scale increase.
Conclusions and recommendations
The prototype SkyGas system at the University currently uses indexed coders on the winches to locate the position of the ropes and, hence the moving head. Although acceptable at the prototype stage, such a system cannot compensate for dynamic changes in rope stretch and supporting post movement and also requires extensive initial manual and labour-intensive positioning of the head for each sampling point. Any future larger scale SkyGas system would benefit greatly from the incorporation of some form of real-time X,Y Z positioning to, firstly, accurately locate the positions of each fixed sampling point and, secondly, to enable construction of a real-time dynamic head position control. Whilst differential GPS is one way of approaching this, the required level of accuracy would probably best be achieved using a terrestrial laser-based scanner with a reflective head-mounted target prism for sub-mm 3D real-time positioning. We would recommend that, at some future date, access to such equipment from the GEF pool would be of benefit not only to the current project but also the wider NERC community. We must emphasise that the opportunity to test alternative (GPS) approaches in the development of the SkyGas system would simply have not been possible without the support of the GEF.
Location of the archived data
The archived data are currently maintained by Andy White, Manager of Technical Support Services in the Electronics Department at the University of York (andy.white@york.ac.uk; Phone: 01904 322412 ). However, the data are considered to be of little value to anyone working outside the current project and are simply stored for referral by the research group at York.
Publications (including conference proceedings)
Ineson et al (2014) Presentation at the annual EGU meeting in Vienna.
Ineson et al (2015) Poster and poster presentation at the COST CLIMANI meeting in Copenhagen, June 2015.
Ineson et al (2014) Progress report at Annual NERC Macronutrients Meeting (Oxford, October 2014).
Ineson et al (in prep.) SkyGas: a novel system for monitoring terrestrial greenhouse gas fluxes reveals diurnal fluxes in nitrous oxide emissions. Global Change Biology, to be submitted in November 2015.